Heat Exchanger Manufacturers in Delhi
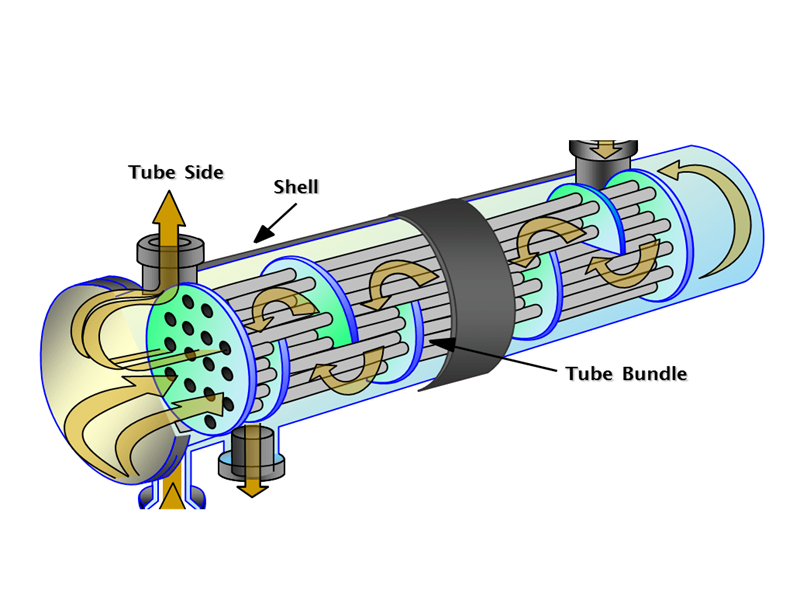
Erika Fluid Power is the best Heat Exchanger Manufacturers in New Delhi. One of the greatest features that you get using our Heat Exchangers is the superior heat transfer efficiency that you get and hence this can be the turning point of our exchangers for your business as well. These are designed in such a way that they can deliver the optimum results. This is the reason why we have integrated some of the best techs into these exchanges as these can give you the maximum surface area for effective heat exchange, which then ensures there is an effective and fast heat transfer between fluids. This efficiency ensures that your systems work at their optimum temperature to improve general performance and productivity.
Heat Exchanger Exporters from Delhi
We are the punctual Heat Exchanger Exporters from Delhi. These are very useful in a range of business settings. These contribute to preventing energy losses within the system by efficiently transferring heat and reducing the amount of energy applied to the system for its desired temperature setting. This increased efficiency reduces running costs and minimizes the impact on the environment, ensuring that sustainability targets are met.
Heat Exchanger Suppliers in India
Consider us for all the needs of your Heat Exchanger Wholesale Suppliers in India. When you choose our Heat Exchangers you can be sure that you are putting your money into a worthwhile investment, you are buying a product that offers optimized performance and reduced operational costs while promoting your sustainability targets. Only trust us to provide the best heat transfer solutions for needs such as yours.
A water-cooled oil cooler is a device used to cool oil in various systems, such as hydraulic systems, engine oil systems, and transmission systems. It consists of a heat exchanger that utilizes water as the cooling medium. The advantages of using a water-cooled oil cooler include efficient heat transfer and the ability to maintain a consistent oil temperature, even under demanding operating conditions. By effectively cooling the oil, it helps prevent overheating, which can lead to lubricant breakdown, reduced system performance, and potential damage to components.
MODEL | LENGTH MM | TUBE LENGTH MM | NO.TUBES | TUBE DIA MM | DIA SHELL MM | PT-1(BSP) | PT-2(BSP) | PT-3(BSP) | MOTOR HP | PUMP FLOW LPM |
HE/WC:EFP:0020 | 525 | 427 | 24 | 9.5 | 140 | 3/4” | 3/4” | 3/8” | 5 H.P | 20 LPM |
HE/WC:EFP:0021 | 700 | 512 | 24 | 9.5 | 140 | 3/4” | 3/4” | 3/8” | 10 H.P | 30 LPM |
HE/WC:EFP:0022 | 750 | 680 | 48 | 9.5 | 167 | 1” | 1” | 1/2” | 12.5 H.P | 40 LPM |
HE/WC:EFP:0023 | 906 | 837 | 48 | 9.5 | 167 | 1” | 1” | 1/2” | 15 H.P | 65 LPM |
HE/WC:EFP:0024 | 1106 | 1037 | 48 | 9.5 | 167 | 1.1/4” | 1” | 1/2” | 20 H.P. | 80 LPM |
HE/WC:EFP:0025 | 853 | 737 | 100 | 9.5 | 220 | 1.1/4” | 1.1/4” | 3/4” | 25 H.P | 110 LPM |
HE/WC:EFP:0026 | 1103 | 987 | 100 | 9.5 | 220 | 2” | 1.1/4” | 3/4” | 30 H.P | 150 LPM |
HE/WC:EFP:0027 | 1303 | 1187 | 100 | 9.5 | 220 | 2” | 1.1/4” | 3/4” | 40-50 H.P | 200 LPM |
HE/WC:EFP:0028 | 1703 | 1578 | 100 | 9.5 | 220 | 2.1/2” | 1.1/4” | 3/4” | 60 H.P. | 240 LPM |
Key Features:-
1. Modular Design:---- >Tube Bundles: Removable tube bundles allow for maintenance and cleaning. • Customizable: Can be designed to meet specific thermal and pressure requirements.
2. Variety of Configurations:---- Flow Arrangements: Available in various flow arrangements (counterflow, parallel flow, crossflow) to optimize heat transfer based on the application.
3. Material Options:---- Construction Materials: Can be made from a wide range of materials, including carbon steel, stainless steel, titanium, and other alloys, depending on the application's requirements.
4. Pressure Ratings:---- High-Pressure Tolerance: Capable of handling both high and low-pressure applications.
5. Temperature Range:---- Wide Operating Range: Suitable for both high and low temperatures, making them versatile for various processes.
6. Compact Design:---- Space Efficiency: Despite their high heat transfer capabilities, they can be designed to be relatively compact.
7. Ease of Maintenance:---- Access to Tube Bundle: The design allows for easy access to the tube bundle for cleaning, inspection, and maintenance.
Advantages:-
1. High Heat Transfer Efficiency:------ Effective Heat Transfer: The design maximizes the surface area available for heat exchange, enhancing overall heat transfer efficiency.
2. Versatility:---- Adaptability: Suitable for a wide range of applications, including heating, cooling, condensing, and evaporating.
3. Scalability:----- Flexible Sizing: Can be scaled up or down in size and capacity to fit various process requirements.
4. Durability:---- Long Service Life: Designed to withstand harsh operating conditions, including high pressures and temperatures, with proper material selection.
5. Cost-Effectiveness:---- Efficiency and Longevity: Offers a cost-effective solution for heat exchange needs due to its durability and efficiency.
6. Reduced Fouling:---- Design Adaptations: Can be designed with features to reduce fouling and scaling, which helps maintain efficiency over time.
7. Safety and Reliability:---- Robust Construction: Built to meet stringent safety and reliability standards, making them suitable for critical applications.
8. Low Maintenance Costs:---- Easy Maintenance: The ability to clean and inspect the tube bundle reduces maintenance downtime and associated costs.
9. Customization Options:---- Tailored Solutions: These can be customized to meet specific process needs, such as special materials for corrosive fluids or unique configurations for space constraints.
10. Flow Distribution:---- Optimized Flow: The shell and tube design allows for effective flow distribution, minimizing thermal gradients and improving overall heat transfer.
Shell and tube heat exchangers are used in a wide range of applications due to their adaptability, efficiency, and robustness. Here’s a detailed look at some of their key applications across various industries:-
• Chemical and Petrochemical Industry • Power Generation • HVAC (Heating, Ventilation, and Air Conditioning)
• Oil and Gas Industry • Food and Beverage Industry • Pharmaceutical Industry • Pulp and Paper Industry
• Marine and Offshore • Metal Processing • Water Treatment • Automotive Industry • Air Conditioning and Refrigeration
PLATE TYPE HEAT EXCHANGER
A type heat exchanger is a type of heat exchanger that uses metal plates to transfer heat between two fluids. These exchangers comprise multiple thin, slightly separated plates with very large surface areas and fluid flow passages for heat transfer. The fluids usually flow in opposite directions through the heat exchanger to maximize heat transfer efficiency.
Key features and advantages of plate-type heat exchangers include:-
- High Heat Transfer Efficiency
- Compact Size
- Flexibility and Scalability
- Easy Maintenance
- Lower Fouling and Maintenance Costs
- Wide Range of Applications
Plate Type Heat Exchanger Application:-
- HVAC Systems: Heating and cooling systems, district heating, and cooling.
- Industrial Processes: Heat recovery, process heating, and cooling.
- Power Generation: Cooling and heating in power plants, including geothermal and biomass.
- Chemical and Petrochemical Industries: Heat exchange in chemical reactions, cooling of process fluids, and temperature control.
- Food and Beverage Industry: Pasteurization, cooling, and heating of food products.
- Pharmaceuticals: Temperature control and heat exchange in drug production processes.
S.No |
Technical Specification |
Description |
1 | Plate Material | MS, Stainless Steel (e.g., AISI 304) to Titanium, Hastelloy, Inconel (for highly corrosive environments) |
2 | Plate Size | 200 mm x 200 mm (8 in x 8 in) to ~1,200 mm x 1,200 mm (47 in x 47 in) |
3 | Number of Plates | 10 plates to ~300 plates |
4 | Heat Transfer Area | 0.5 m² (5.4 ft²) to ~1,500 m² (16,150 ft²) |
5 | Flow Rate | 0.1 m³/h (0.4 gpm) to ~10,000 m³/h (44,000 gpm) |
6 | Pressure Rating | 6 bar (87 psi) to ~30 bar (435 psi) |
7 | Temperature Range | 10°C (14°F) (with special designs) to ~200°C (392°F) |
8 | Plate Gap | 10°C (14°F) (with special designs) to ~200°C (392°F) |
9 | Overall Dimensions | 500 mm x 500 mm x 500 mm (20 in x 20 in x 20 in) to ~3,000 mm x 3,000 mm x 3,000 mm (118 in x 118 in x 118 in) |
10 | Leakage Rate | 0.1 L/h (depending on design and testing) to ~0.5 L/h (for very tight designs) |
11 | Thermal Efficiency | 70% to ~95% |
12 | Cleaning and Maintenance | Manual cleaning with chemical agent to Automated cleaning systems (e.g., CIP - Cleaning In Place) |
Brazed Plate Heat Exchangers:-
Brazed Plate Heat Exchangers are a type of heat exchanger that utilizes a series of thin, corrugated metal plates, which are brazed together to create a compact and efficient heat transfer device. Here’s an in-depth look at their features, advantages, and typical applications:
1. Size and Dimensions: Minimum:-
- Plate Thickness: Typically around 0.4 mm (0.0157 inches).
- Plate Width: Starting from about 200 mm (7.87 inches).
- Plate Length: Starting from about 500 mm (19.69 inches).
2. Size and Dimensions: Maximum:-
- Plate Thickness: Up to 1.5 mm (0.059 inches) or more.
- Plate Width: Can exceed 600 mm (23.62 inches) depending on design.
- Plate Length: Can exceed 1,200 mm (47.24 inches) for larger units.
2. Heat Transfer Area: Around 0.5 m² (5.38 ft²) for small units. To exceed 100 m² (1,076 ft²) for large, industrial-scale units.
3. Flow Rates: Typically around 1 m³/h (4.4 GPM) for small applications. To exceed 100 m³/h (440 GPM) for larger systems.
4. Pressure Ratings: Typically around 6 bar (87 psi) for smaller or less demanding applications. It can exceed 30 bar (435 psi) for high-pressure applications.
5. Temperature Ratings: Typically around -40°C (-40°F) for low-temperature applications. To Can exceed 200°C (392°F) for high-temperature processes.
6. Material of Construction: Commonly stainless steel (e.g., 304 or 316 grade). It can include more specialized materials such as titanium or exotic alloys for corrosive environments.
7. Connections Inlet/Outlet Sizes: Typically starting from DN15 (1/2 inch) or similar small sizes. To exceed DN150 (6 inches) or more for larger units.